Storage tank protection – a challenging endeavour
The storage of flammable liquids with a high vapour pressure, in particular crude oil, poses challenges in view of fire prevention and safety.
Atmospheric storage tank fires are relatively rare, but because they store large amounts of flammable liquid in them, they can have catastrophic consequences. In a recent study, the causes and costs of 104 accidents were classified. The initiating events in 38% of the accidents were environmental factors, 20% equipment factors, 15% operational factors (human error), 13% domino effect, 10% maintenance factor and 4% terrorist attack. The average cost for accidents that have produced domino effects was approximately 24,181,673 $, and for accidents without domino effects, it was 205,191,298 $. [1]
An unprotected fire incident can quickly result in large-scale fires, explosions and thick vapour clouds; all of which cause danger to infrastructure, people and the environment. Business interruption with impact on various stakeholders is also a risk in this context.
How to protect storage tanks?
Owners and operators of crude oil storage facilities have several options to mitigate fire events. NFPA 30 (Flammable & Combustible Liquids Code) provides certain guidance; but in addition to codes and standards, owners and operators may want to consider a risk-based approach.
For example, should they let the fire burn out the stored fuel without any fire-fighting activities at the burning tank or maybe couple this rather passive approach with limited protection measures in which they cool the surrounding infrastructure (tanks, process equipment, etc.) to prevent escalation of the fire event (i.e. to prevent so-called “domino effects”). Or, they decide to actively attack the fire, by using fixed and/or mobile fire protection systems to suppress the fire. Fixed foam suppression systems typically consist of foam storage tanks, proportioning/mixing devices and foam discharge devices, the latter located at the top of the tank (e.g. foam chambers).
[1] Ahmadi, O., Mortazavi, S.B. & Mahabadi, H.A. Review of Atmospheric Storage Tank Fire Scenarios: Costs and Causes. J Fail. Anal. and Preven. 20, 384–405 (2020). https://doi.org/10.1007/s11668-020-00846-5
Protect flammable liquid storage tanks
UL Listed and FM Approved foam chambers, makers and pourers from Viking
These are your options to protect flammable liquid storage tanks and surrounding bund areas, and as such, to control and suppress fires involving class B hydrocarbon and polar solvent liquids.
Performance and approval compliance can be ensured when installing and using these products with other Viking foam system components.
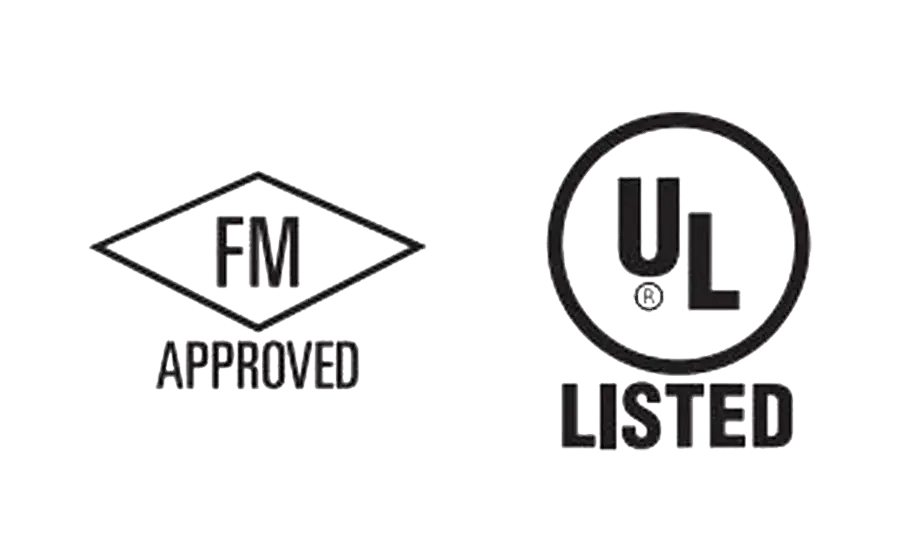
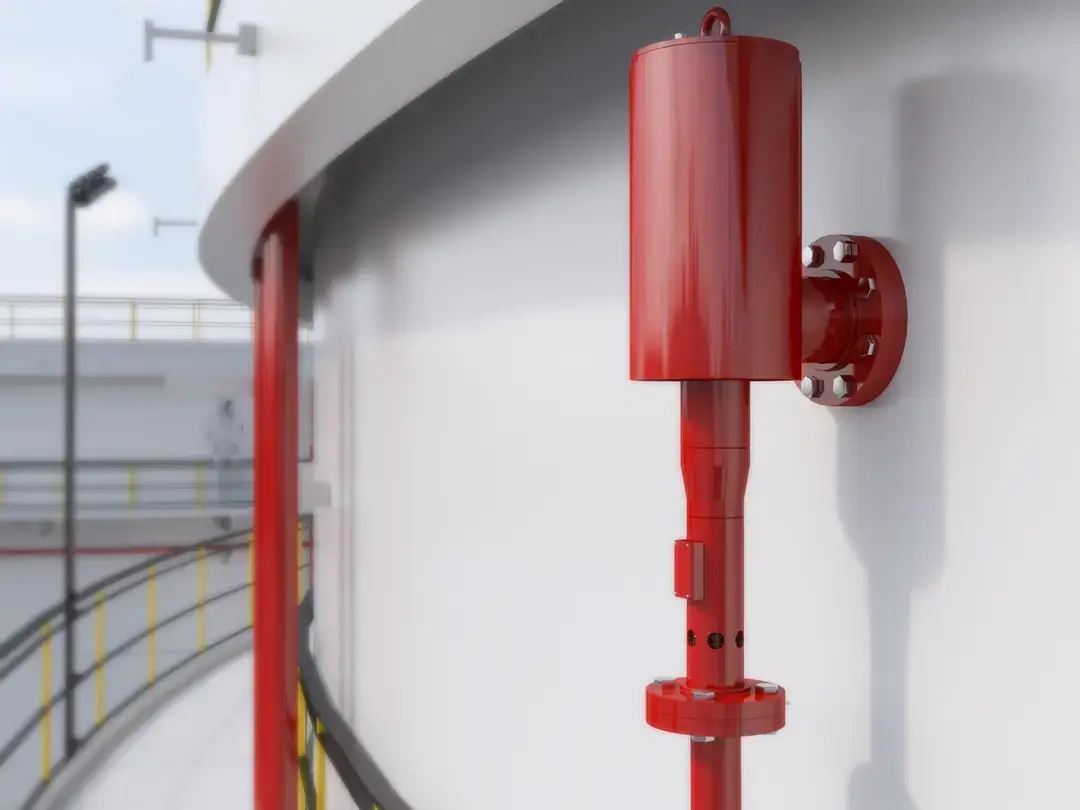
Viking VFC foam chamber at tank
Foam chambers
Features and advantages
- Foam chambers model VFC in 2.5”, 3”, 4” and 6” inlet sizes
- UL Listed & FM Approved with a range of Viking and Fomtec branded foam concentrates
- Tested and approved with “ARK” polar solvent focused alcohol resistant fluorine free foam
- Tested and approved with “USP” hydrocarbon focused fluorine free foam
- Stainless steel 316 version also available with UL Listing & FM Approval
- Galvanization and other special coatings available on request
- Competitive flow rate and pressure range for design flexibility as opposed to single data point products
Foam makers & pourers
Features and advantages
- Foam makers model VFM in 1.5″, 2.5″, 3″ and 4″ inlet sizes
- UL Listed & FM Approved with a range of Viking and Fomtec branded foam concentrates
- Dedicated foam pourer to ensure gentle application using the bund wall – part of the approved and tested assembly
- Tested and approved with “ARK” polar solvent focused alcohol resistant fluorine free foam (SFFF)
- Tested and approved with “USP” hydrocarbon focused fluorine free foam (SFFF)
- Stainless steel 316 version also available with UL Listing & FM Approval (VFM only)
- Galvanization and other special coatings available on request
- Competitive flow rate and pressure range for design flexibility as opposed to single data point products
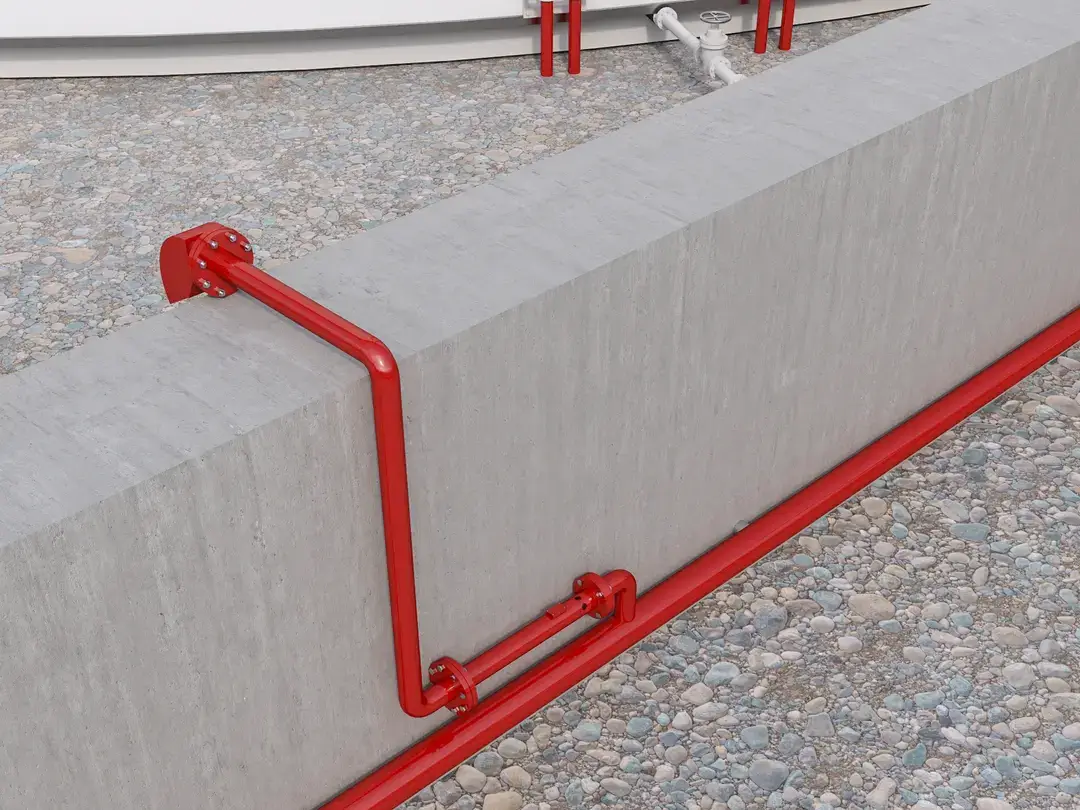
Viking foam maker and pourer on bund
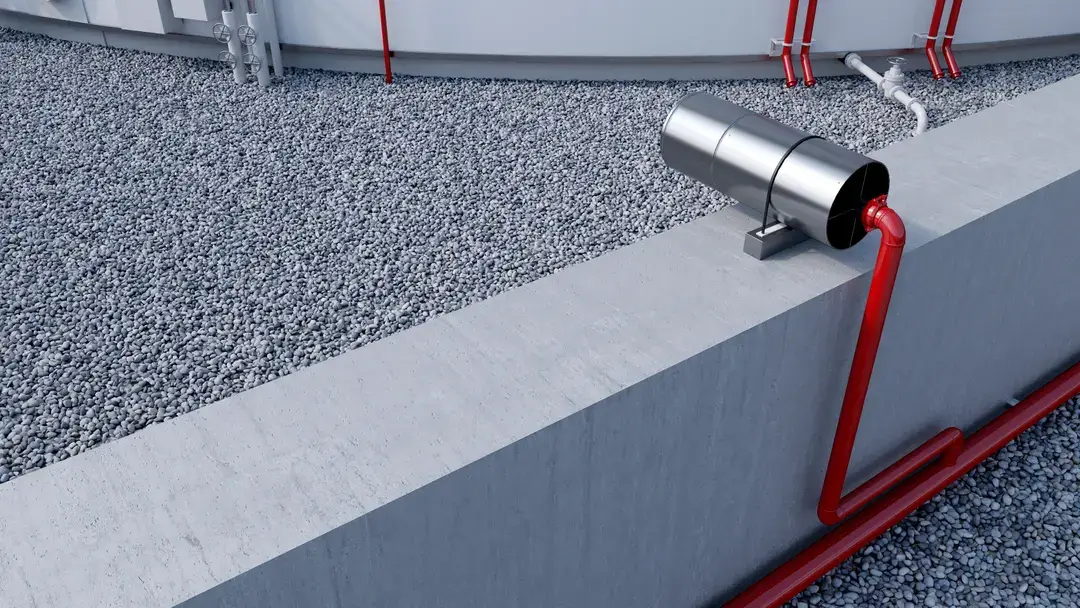
Medium expansion foam generator on bund
Medium expansion foam generators
Features and advantages
- Medium expansion model GM in 1.5″, 2″, 2.5″, and 3″ inlet sizes
- Suitable for use with a range of Viking and Fomtec branded foam concentrates
- Tested with fluorine free foam (SFFF)
- Stainless steel 304 as standard
- For use in total flooding systems where a certain risk volume needs to be filled (3D fires…)
- For use in local application systems where an area/density approach is required
Note: Performance and discharge characteristics are pressure and foam concentrate specific.
Foam chambers & makers with assured performance
Viking foam chambers and foam makers are used for the protection of flammable liquid storage tanks, surrounding bund areas and other dyke protection. Viking foam chambers and makers have been rigorously tested to ensure the correct foam expansion and drainage times are achieved which is vital in the control and suppression of fires involving class B hydrocarbon and polar solvent liquids. It is recommended that Viking foam chambers and makers are used with other Viking foam system components to ensure performance and approval compliance.
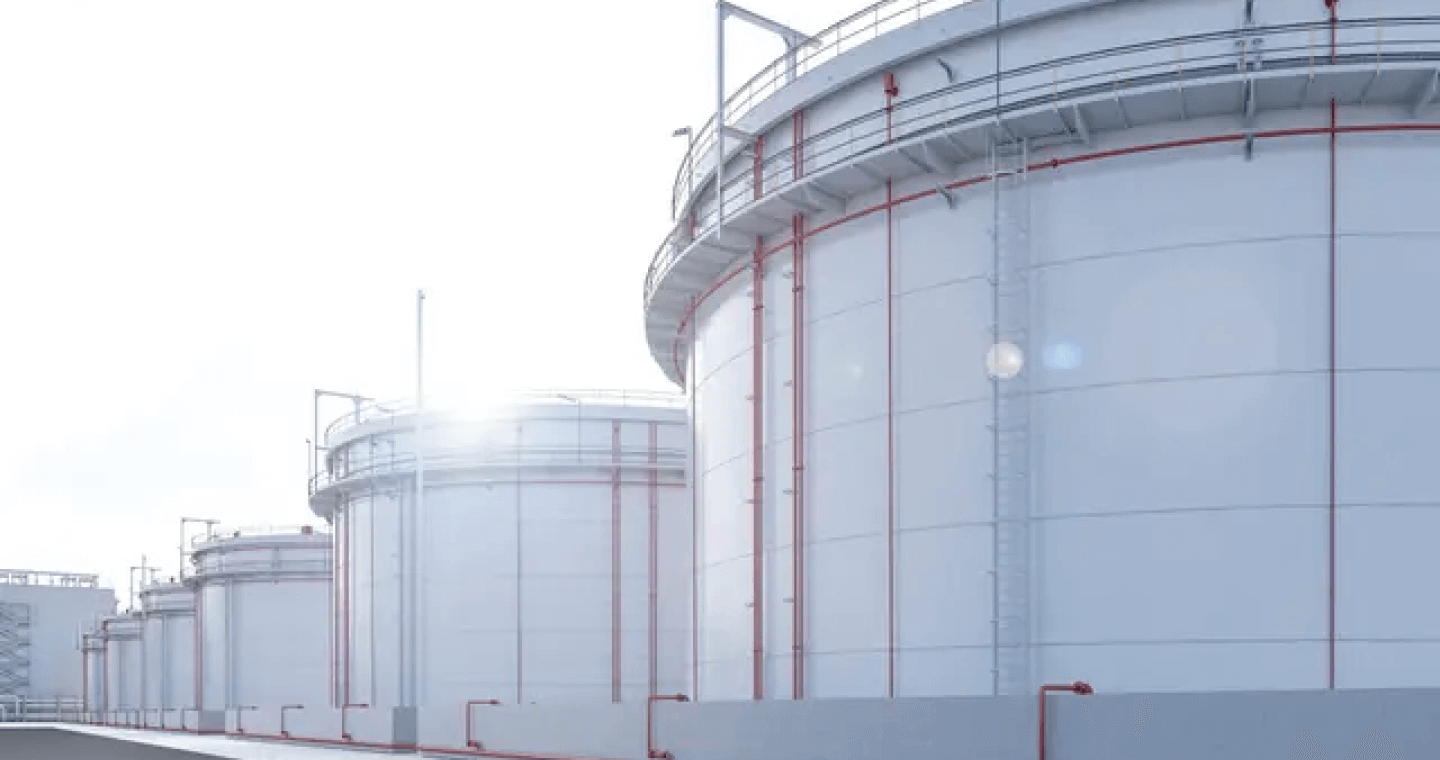
Tank protected by Viking foam chamber, bund area by Viking foam maker and pourer
Downloads
Foam Systems
Leaflet
Languages
Foam Systems
Product sheet
Languages
Foam Systems
Data page
Languages
Foam Systems
Product sheet
Languages
Foam Systems
Data page
Languages
Foam Systems
Product sheet
Languages
Foam Systems
Technical bulletin
Languages
Additional tank protection products
Viking offers additional tank protection products, such as rimseal foam pourers, Quickseal floating roof tank system, and medium and high velocity spray nozzles.
Note: “SFFF compatible” refers to this product as being part of a SFFF Foam system that has been tested to recognised standards. Not all configurations are available. Please consult technical data and/or the Approval/Listing for usage requirements. SFFF stands for synthetic fluorine free foam.
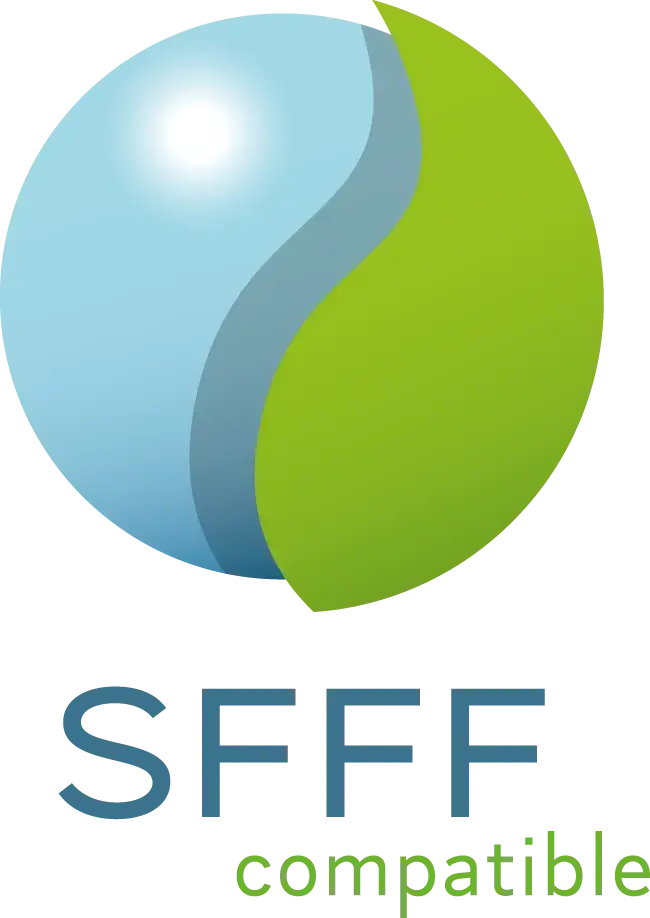
Image source: Viking S.A.